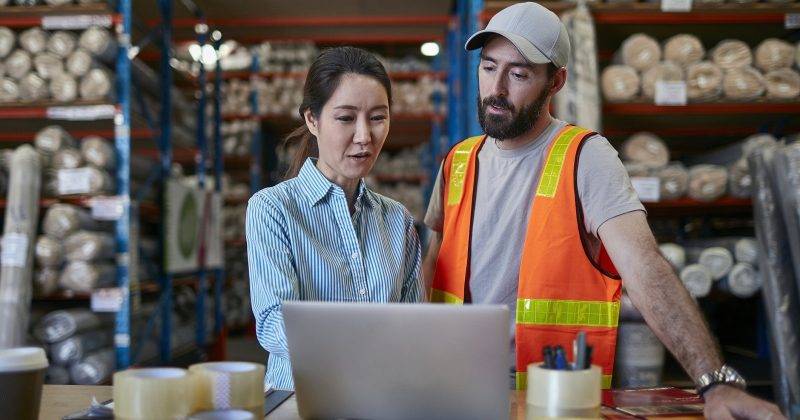
Wholesale Distribution
Wholesale distributors need warehouse management solutions so that their stock is managed as efficiently as possible.
If you’re looking for a way to offer great customer service, reduce turnover and inspire higher-performing employees in your warehouse, it’s time to examine the versatility of a warehouse management system like PathGuide’s Latitude WMS. For more information about Latitude, Latitude Manifest & Shipping System and Advanced VMI, request a free demo today.
What types of industries use Latitude WMS?
Wholesale distributors need warehouse management solutions so that their stock is managed as efficiently as possible.
Latitude WMS provides retail operations with the kind of inventory control not possible before, effectively contributing to the bottom line.
Latitude WMS can take the fear out of your everyday warehouse management, especially if you’re an electrical distributor.